product
contact
Landline:+860374-6621138
Phone:+8613949836393
Phone:+8613938770929
Mailbox:fuxingzhuzao@126.com
Addres:Xiyang Industrial Zone, Changge City, Henan Province

Cutter head body
Product details
Cutter head body
In the field of construction and civil engineering, the cutter head body plays a crucial role in the operation of tunnel boring machines (TBM). This essential component is responsible for cutting through various types of rock and soil to create tunnels for transportation, water supply, or other infrastructure projects. Let's delve deeper into the importance and functions of the cutter head body.
The cutter head body is typically located at the front of the TBM and is equipped with a rotating cutting wheel or disc. This cutting wheel is embedded with cutting tools such as disc cutters, which are designed to break and excavate the rock or soil in front of the TBM. The cutter head body is connected to the main drive system of the TBM, which provides the necessary power and torque to rotate the cutting wheel at the required speed.
One of the key functions of the cutter head body is to maintain the stability of the tunnel face during excavation. As the TBM advances, the cutter head body exerts pressure on the rock or soil in front of it, creating a stable face that prevents collapse or cave-ins. The cutter head body also helps to control the size and shape of the tunnel cross-section, ensuring that the tunnel is excavated to the required dimensions.
Another important function of the cutter head body is to remove the excavated material from the tunnel face. This is typically done using a system of conveyors and muck buckets, which transport the excavated material from the cutter head body to the rear of the TBM for disposal. Efficient removal of excavated material is essential to prevent blockages and maintain the productivity of the TBM.
The design of the cutter head body is crucial to its performance and efficiency. The cutting tools must be carefully selected and maintained to ensure effective cutting and excavation. The shape and size of the cutter head body should be optimized to minimize energy consumption and wear on the cutting tools. Additionally, the cutter head body must be equipped with a robust bearing system to withstand the high forces and pressures encountered during excavation.
In recent years, advancements in technology have led to the development of more sophisticated cutter head bodies. Some TBMs are now equipped with cutter head bodies that can be adjusted or customized to suit different geological conditions. For example, cutter head bodies with interchangeable cutting tools allow operators to adapt to changing rock types or ground conditions without the need for costly downtime or maintenance.
Overall, the cutter head body is a critical component of tunnel boring machines, enabling efficient and safe excavation of tunnels for various infrastructure projects. As technology continues to advance, we can expect further improvements in the design and performance of cutter head bodies, leading to faster and more cost-effective tunnel construction.
keyword:
Cutter head body
Production equipment
We currently have two fully automatic static pressure horizontal molding production lines, one 148 shock pressure molding production line, CNC machine tools, drilling, milling and other equipment, totaling more than 200 sets
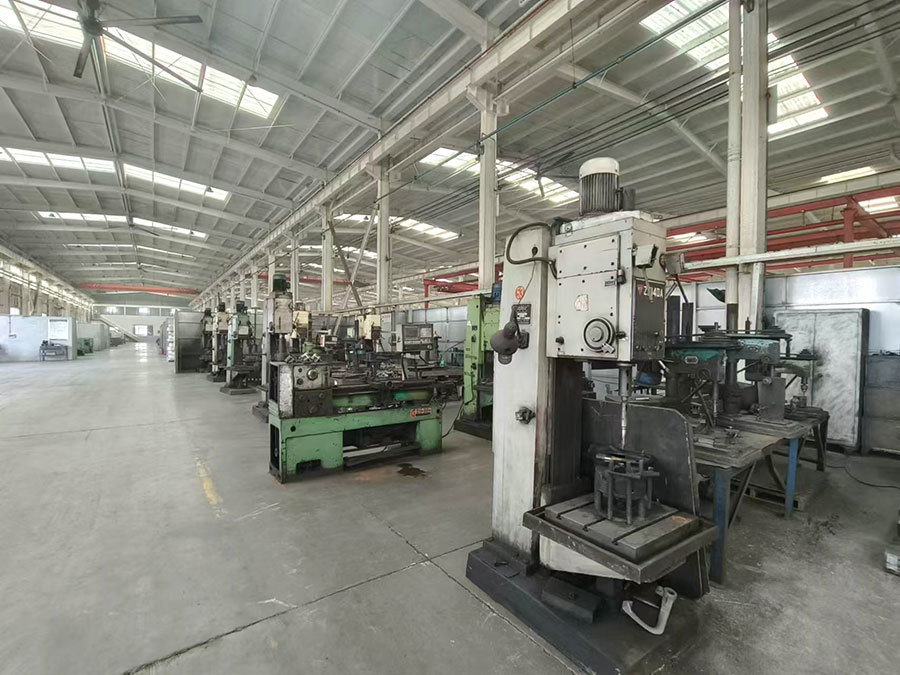
Production Equipment
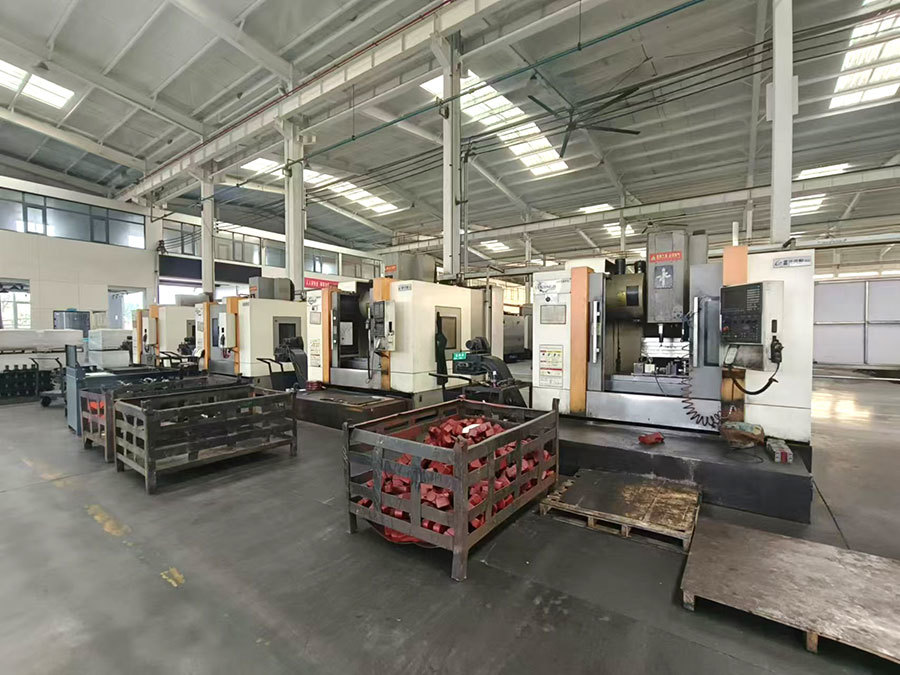
Production Equipment
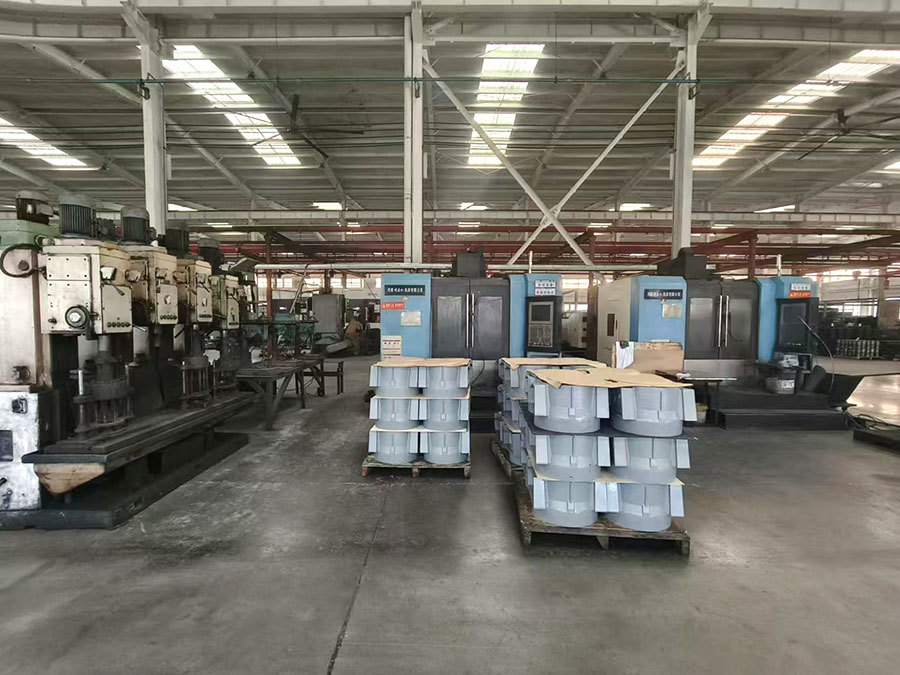
Production Equipment
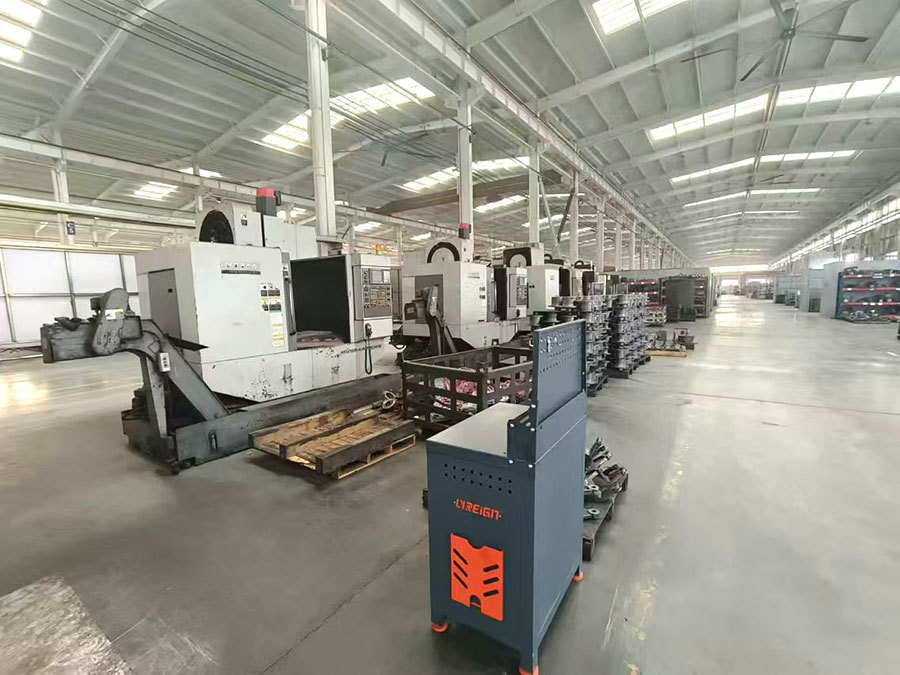
Production Equipment
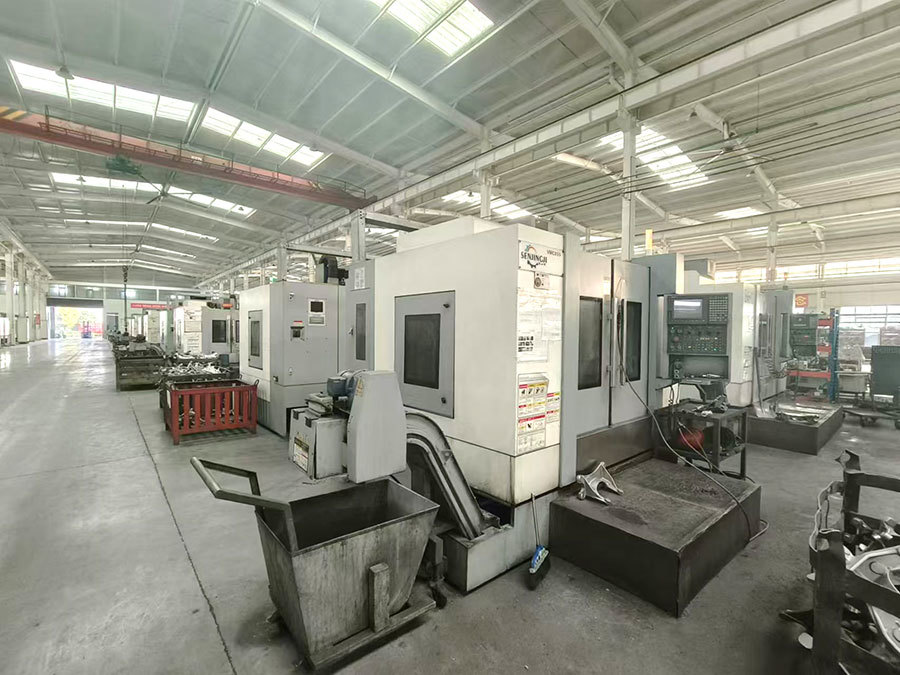
Production Equipment
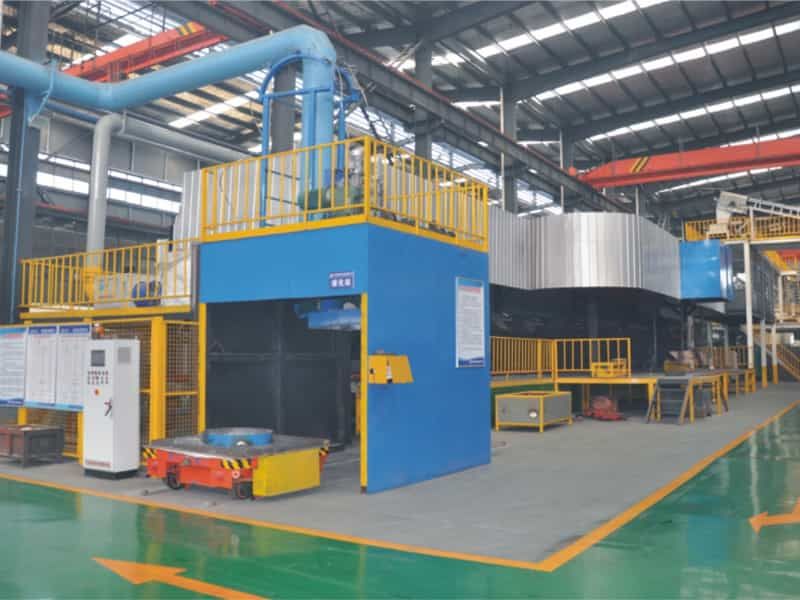
Processing equipment
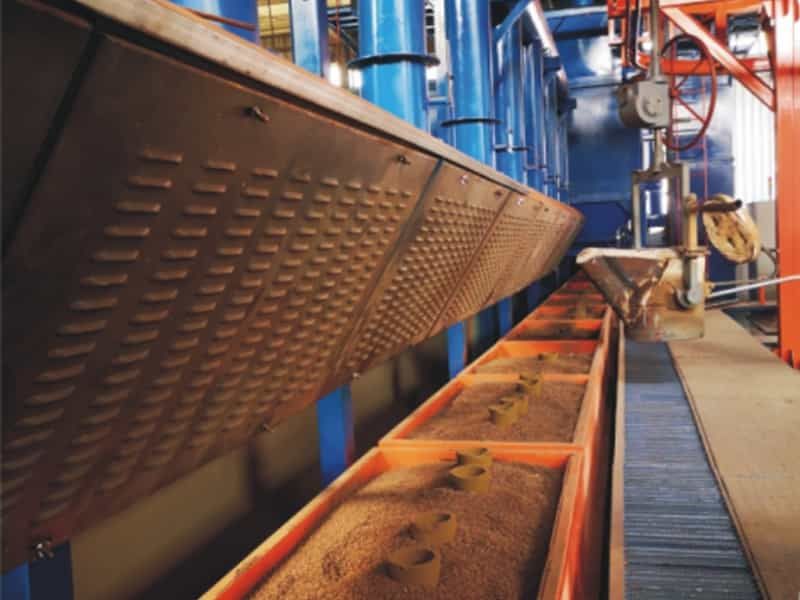
Processing equipment
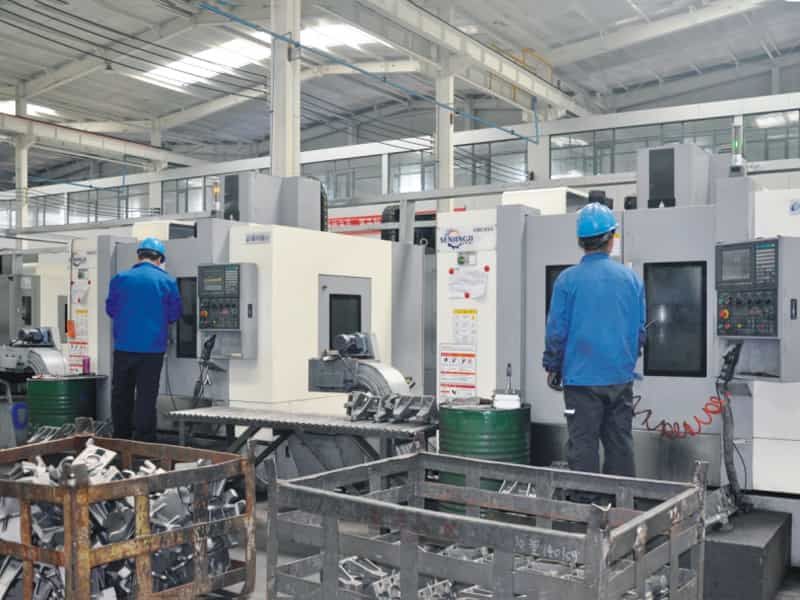
Processing equipment
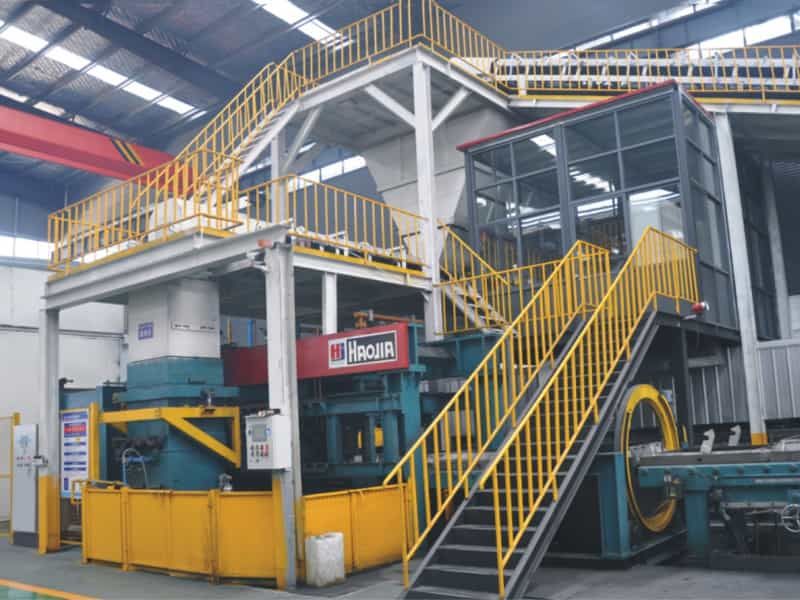
Processing equipment
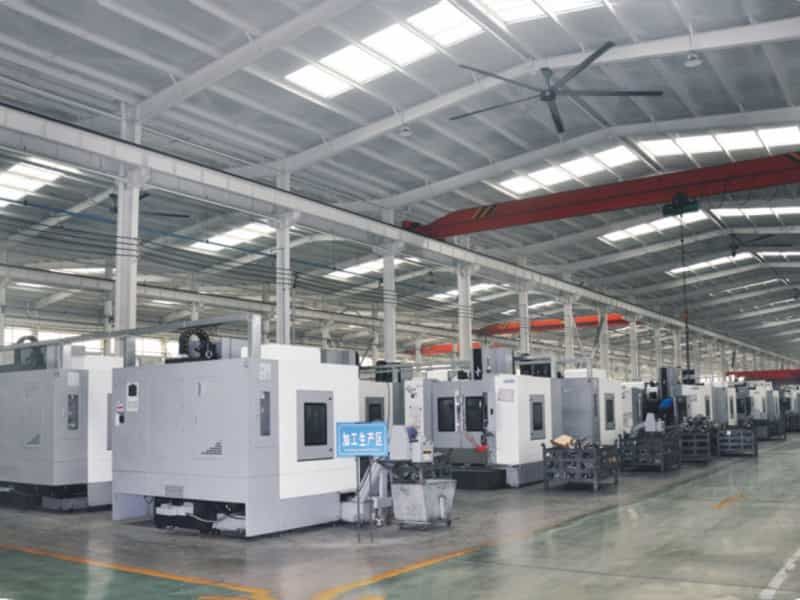
Processing equipment
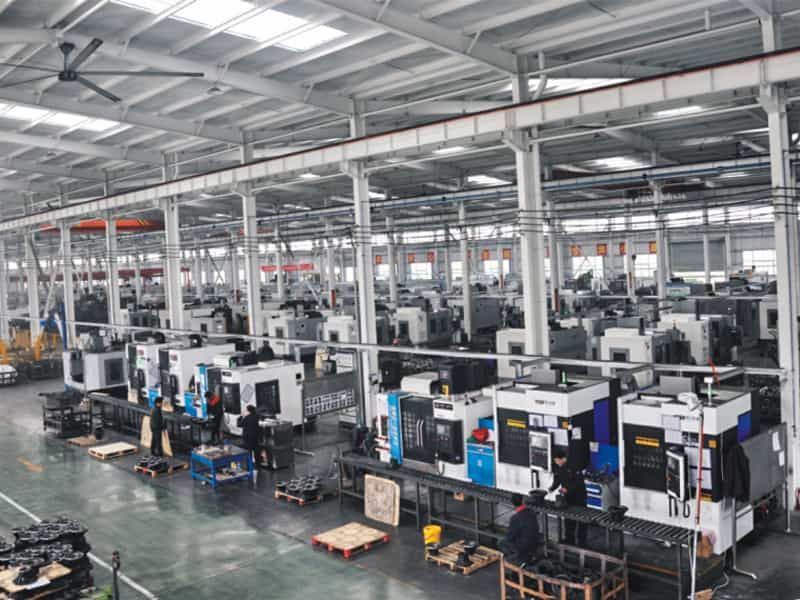
Processing equipment
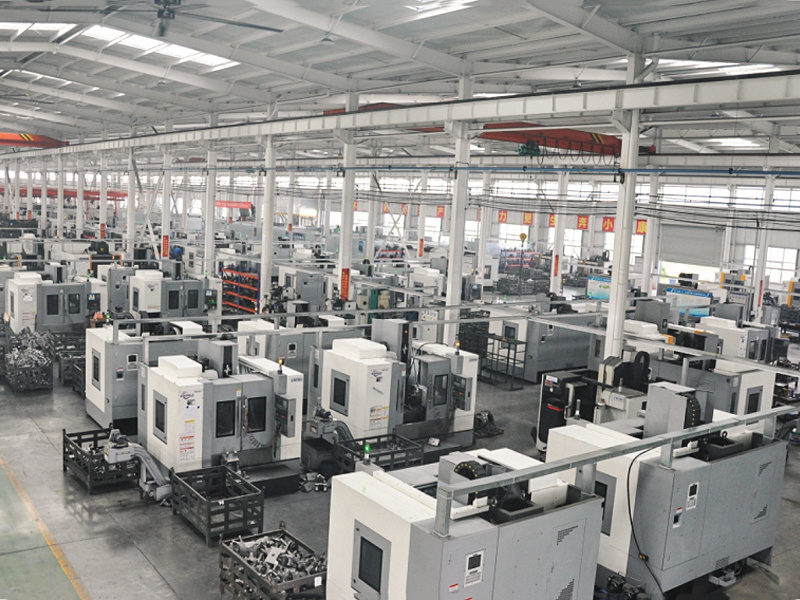
Processing equipment
Instrumentation
We have a complete set of casting testing and inspection equipment, including over 20 high-precision testing and inspection instruments such as vacuum direct reading spectrometer and carbon sulfur analyzer
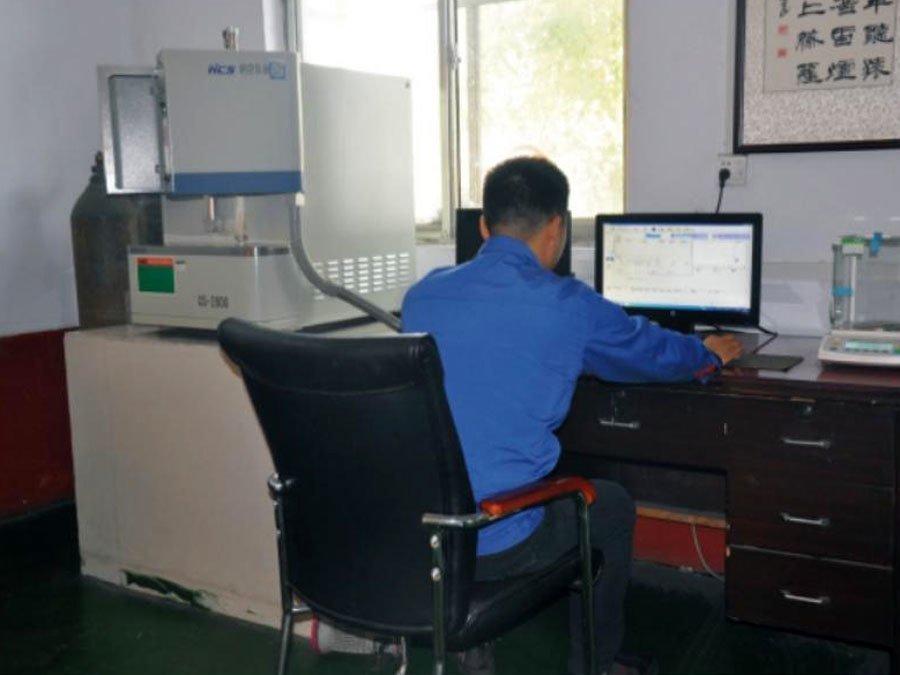
Test equipment
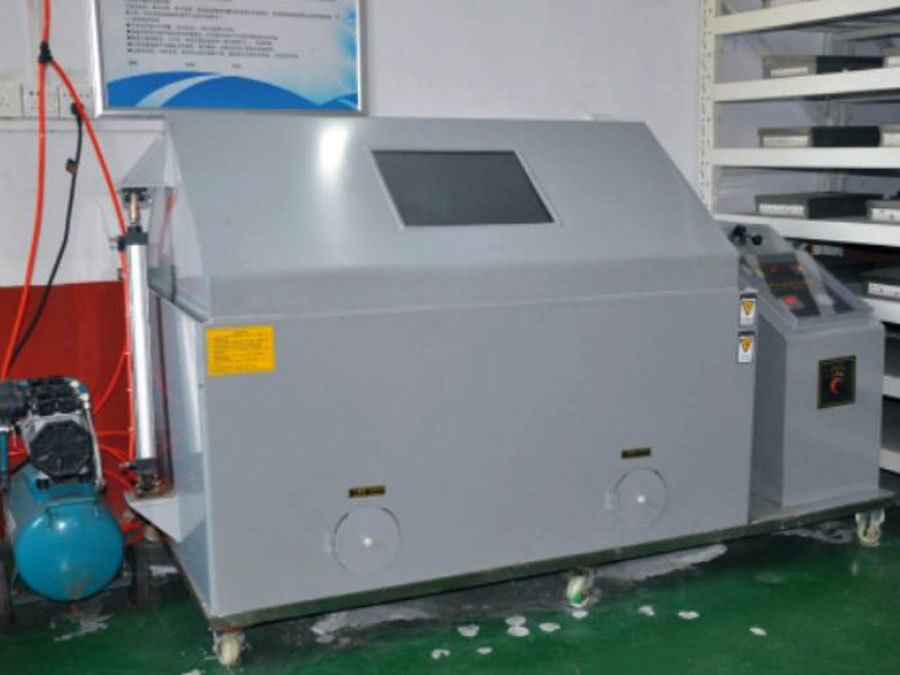
Test equipment
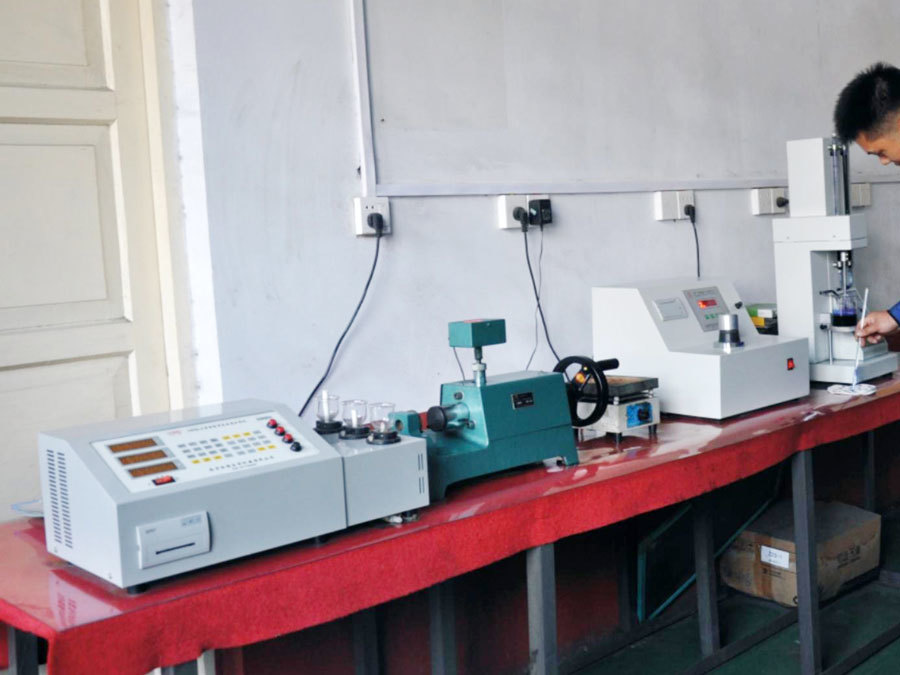
Test equipment
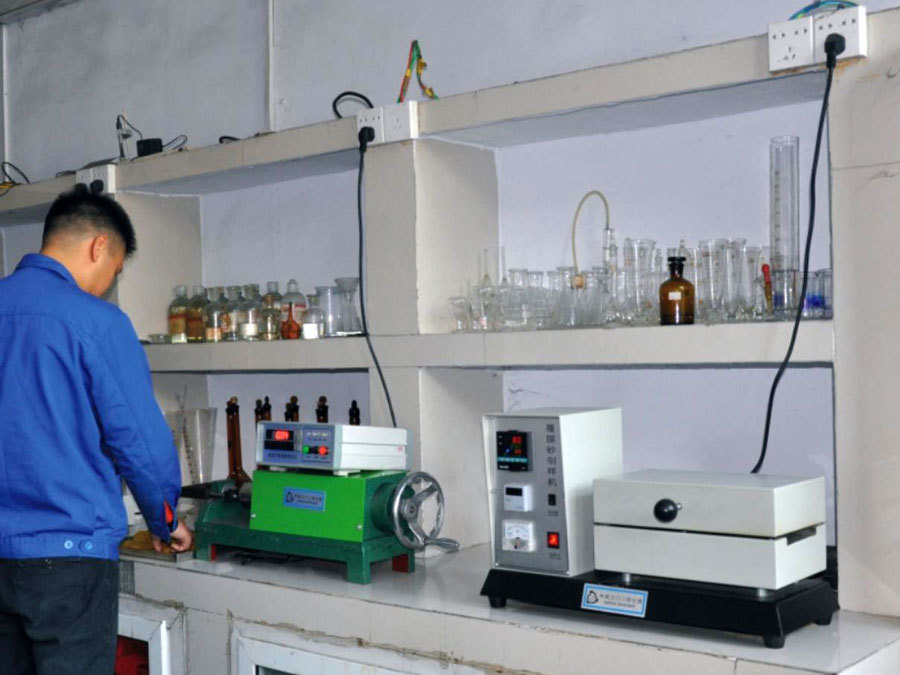
Test equipment
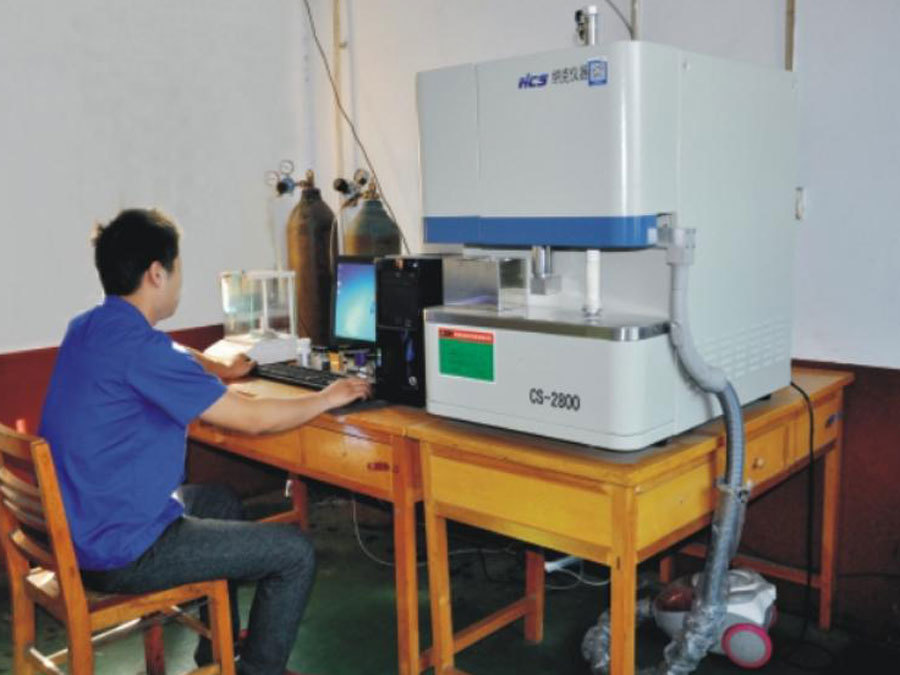
Test equipment
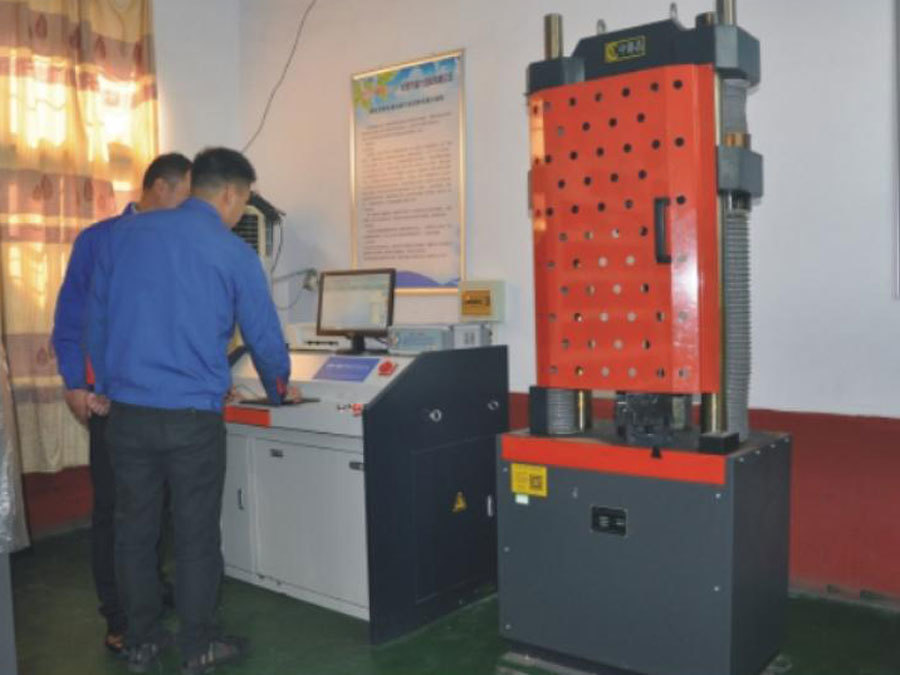
Test equipment
BLOG
Ductile iron casting plays a crucial role in modern industrial manufacturing.
Ductile iron castings occupy a pivotal position in many industrial fields.
Ductile iron, an alloy that occupies an important position in the field of materials science!
Turbocharged vehicle maintenance: high cost of repairing core components
What technology is used to create car wheels? Is it durable and long-lasting?
How is the forging and replacement of automotive parts done?
Related products
Online Message
If you have any suggestions, please leave a message or send an email to us, and we will reply to you within 1 working day after receiving the message email.